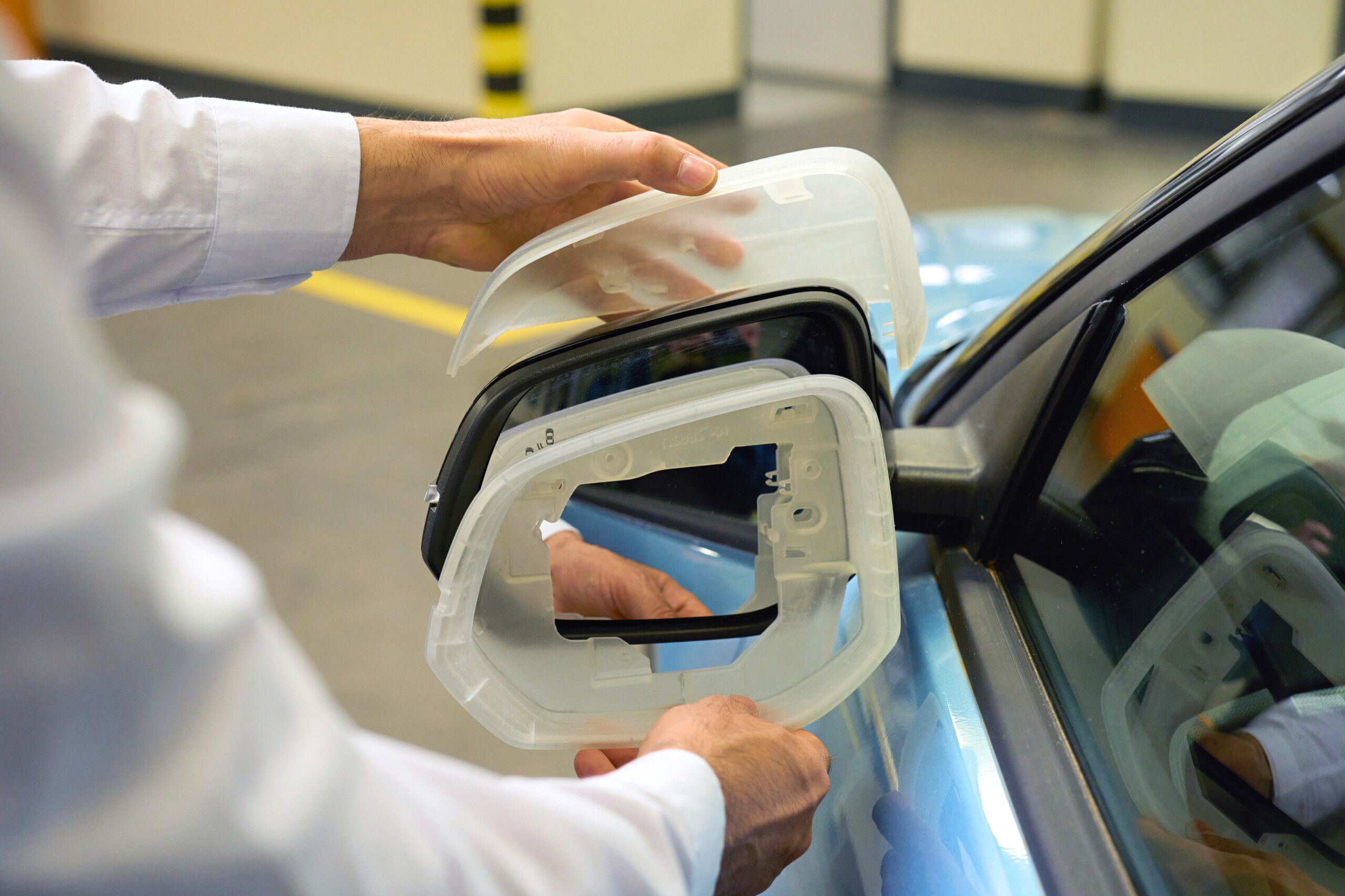
Ford and Formlabs reveal how 3D printing contributed to the Electric Explorer
SLA and SLS 3D printers generated prototypes and tooling inserts to speed up electrification.
When the Formlabs Type 4 debuted earlier this yr, the corporate promised sooner, extra dependable 3D printing for prototyping and manufacturing. Immediately, we’re getting a brand new instance of what which means with a reveal from one of many Type 4’s beta testers: Ford Motor Firm.
The automaker has made in depth use of 3D printing in designing the brand new Electrical Explorer, together with the Type 4 in addition to the Fuse 1+ and Type 3L. As well as, Ford’s designers mixed these additive manufacturing instruments with extra standard subtractive manufacturing, comparable to milling, and injection molding.
In keeping with Ford, the most recent era of Formlabs printers has enabled designers to satisfy requests in below 24 hours, even these from different services, offered they’re in vary of in a single day transport. Stereolithography (SLA) enabled the corporate to validate designs of each inside and exterior elements, such because the sideview mirror meeting. Selective laser sintering (SLS) assisted with mechanical testing, significantly for the advanced design of the Electrical Explorer’s charging port.
“For this charging cowl, it was necessary to make use of SLS, primarily based on the truth that we would have liked a purposeful half that may allow us to check the mechanisms,” mentioned Bruno Alves, additive manufacturing skilled and tooling specialist at Ford in a media launch. “It’s a extremely advanced design that we aren’t capable of produce in another manner. We can’t mill this half. We can’t use injection molding to provide just a few samples. So one of the best ways is to print in a cloth that we are able to check bodily.”
Even when Ford’s designers did use injection molding, 3D printing proved to be a worthwhile complement. The Electrical Explorer’s door deal with design requires two rubber elements for damping and insulation and, whereas these had been injection molded, the designers additionally 3D printed inset molds for his or her in-house injection molding machine.
“This was a posh course of as a result of we’re utilizing a number of inserts and there are additionally a number of totally different designs that would have a number of iterations every,” mentioned Alves. “Usually, exterior injection molding will take perhaps two or three months. Internally, utilizing additive manufacturing, we are able to pace up the method to perhaps two weeks, three weeks most. For this challenge, if we had to make use of exterior instruments, it could have been far more time-consuming and we’d not have been capable of ship the elements on time.”
Much more than quantity or repeatability, pace is essentially the most crucial variable in 3D printing with regards to adoption, particularly for prototyping. As this story of the design work for Ford’s Electrical Explorer suggests, it’s additionally important for accelerating electrification.