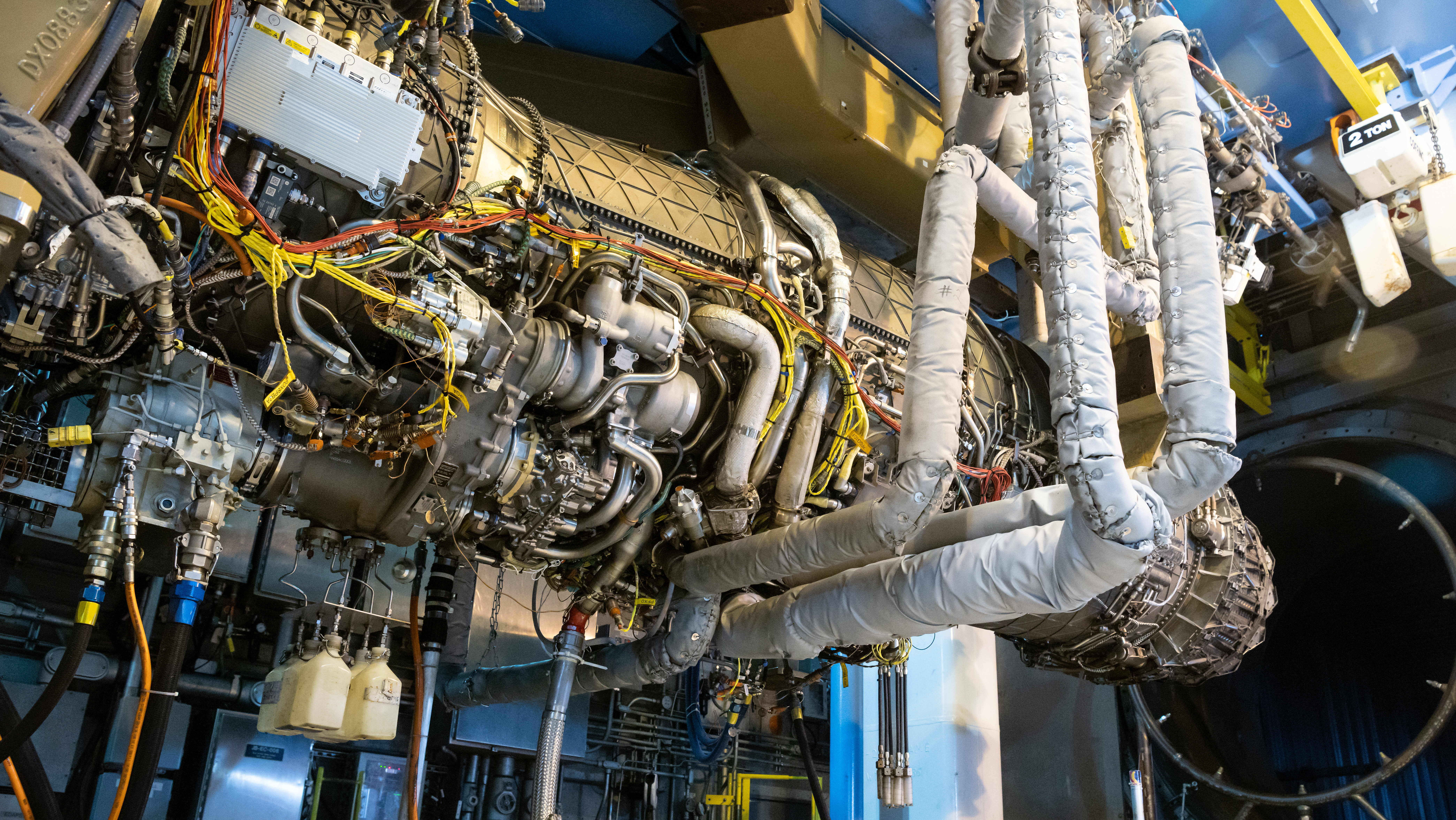
Pratt plans 3-D printed parts for F-35 engine
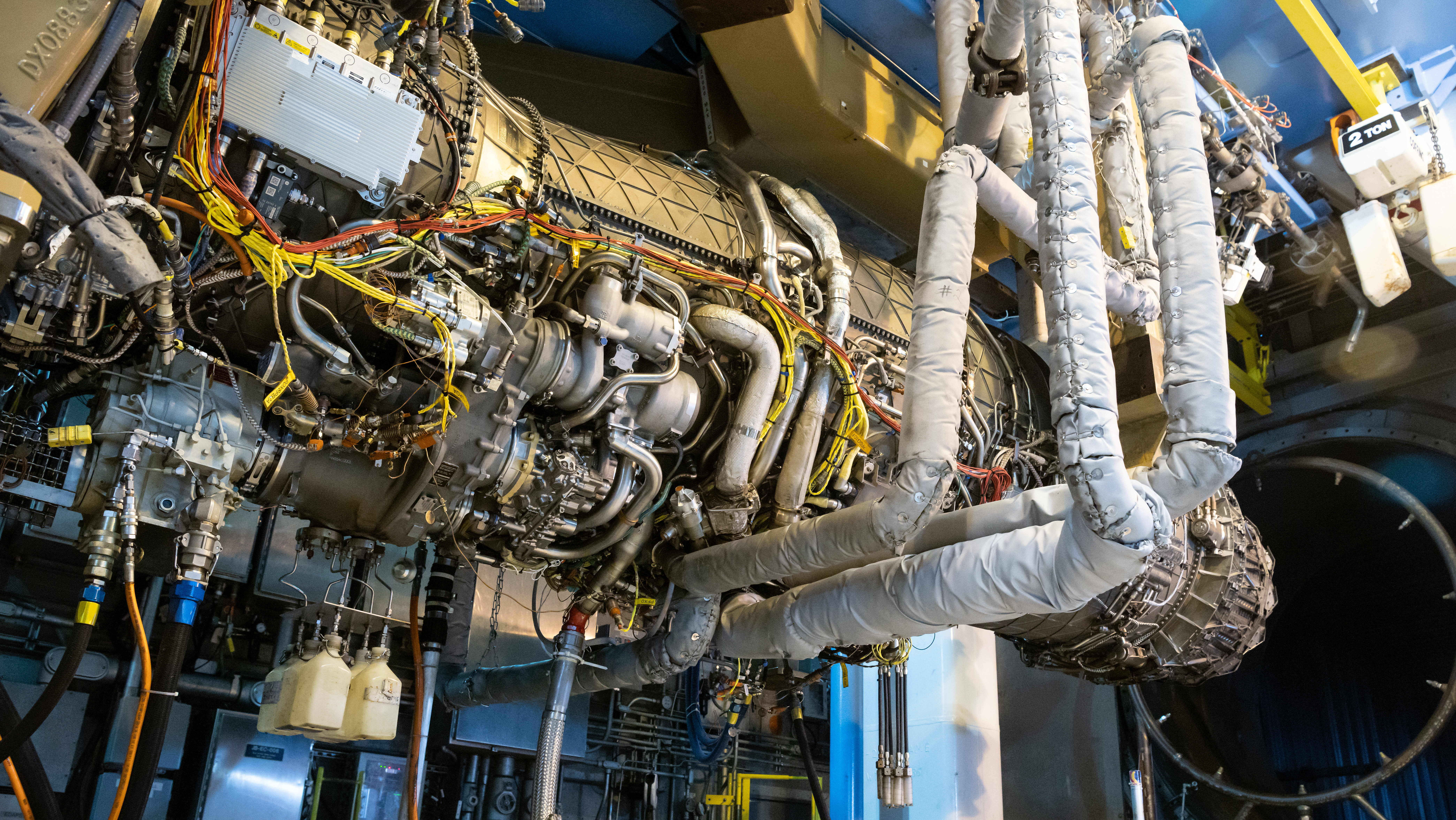
A Pratt & Whitney F135 engine hangs in Arnold Engineering Growth Complicated (AEDC) Sea Stage Check Cell 3 at Arnold Air Drive Base, Tenn., between take a look at runs Sept. 2, 2021. (U.S. Air Drive photograph by Jill Pickett)
FARNBOROUGH 2024 — Pratt & Whitney’s efforts to include additively manufactured components into its merchandise now extends to the F135 engine, the powerplant of the F-35 Joint Strike Fighter, in response to an organization government.
“We’re engaged on fairly a little bit of restore growth,” Jill Albertelli, Pratt’s president of navy engines, solely instructed Breaking Protection in an interview over the weekend. “Issues like additive [manufacturing] can even assist in restore growth exercise, and we’ve a plan” to include the know-how into the F135, she mentioned.
In accordance with a Pratt assertion, the corporate in 2018 started work to additively manufacture the engine’s turbine exhaust case trailing edge field, which directs exhaust gasses. The approach departs from the usual methodology referred to as hydroforming, Pratt mentioned, the place high-pressure fluid is used to kind steel plates.
Additive manufacturing, or 3D-printing, works by fusing steel powders collectively one skinny layer at a time. Guided by a digital design, the approach can supply enhancements like sooner manufacturing velocity, decrease value and simplifying a system by lowering the variety of components essential, versus conventional strategies that require carving out quite a few elements from bigger items of present materials. 3D-printed components can even scale back weight, a bonus for plane.
Introducing new materials into any design requires further certification, Albertelli mentioned.
Moreover the F135, Pratt can also be trying to harness additive manufacturing on easier engines just like the TJ150 with a watch towards alternatives just like the Air Drive’s Collaborative Fight Plane (CCA) initiative. Pratt has been working to completely manufacture the powerplant utilizing additive methods, and has to date lowered the variety of engine components from 50 to “lower than 5,” in response to Albertelli.
“Because the US Air Drive did an evaluation on the protection industrial base, additive manufacturing is one thing that they highlighted considerably,” to assist scale back provide chain burdens, Albertelli mentioned in a Monday briefing on the Farnborough air present. The know-how may assist the service’s CCA effort that seeks to mass produce low-cost drones.
RELATED: GE and Kratos unveil new engine ‘household,’ aimed toward cruise missiles, CCA
A more recent configuration of the TJ150, which incorporates additively manufactured rotating components, will start testing in 2025, which might be adopted by altitude and flight testing, Albertelli mentioned.
Pratt is in dialogue with clients concerning the engine, and underlying additive know-how, for platforms like CCA, Albertelli added. Between home and worldwide demand, orders for platforms like CCA drones, and attendant propulsion programs, may “undoubtedly” attain into the 1000’s, she mentioned.